Jar Bottle Fillers | Jar Bottle Filling Machines
Modern bottle filling machines are often inline (in production) automated and can include additional features such as cap placing, cap sealing, and label application. The automation allows for higher accuracy, greater speed, and minimal product waste compared to manual filling methods.
Liquid Bottle Filling Machines
A Liquid Bottle Filling Machine is designed to automate the process of filling bottles with liquid or products. These machines are commonly used in industries such as energy drinks, cough syrups, lotions, laundry detergents, sauces, lubricants, liquid fertilizers, Engine oils, and liquid medications, where large quantities of liquids need to be efficiently packaged.
There are different types and configurations of liquid bottle filling machines available, depending on the specific requirements of the industry and the type of liquid being filled. These machines can vary in terms of filling method (gravity, piston, vacuum, etc.), filling capacity, and automation level.
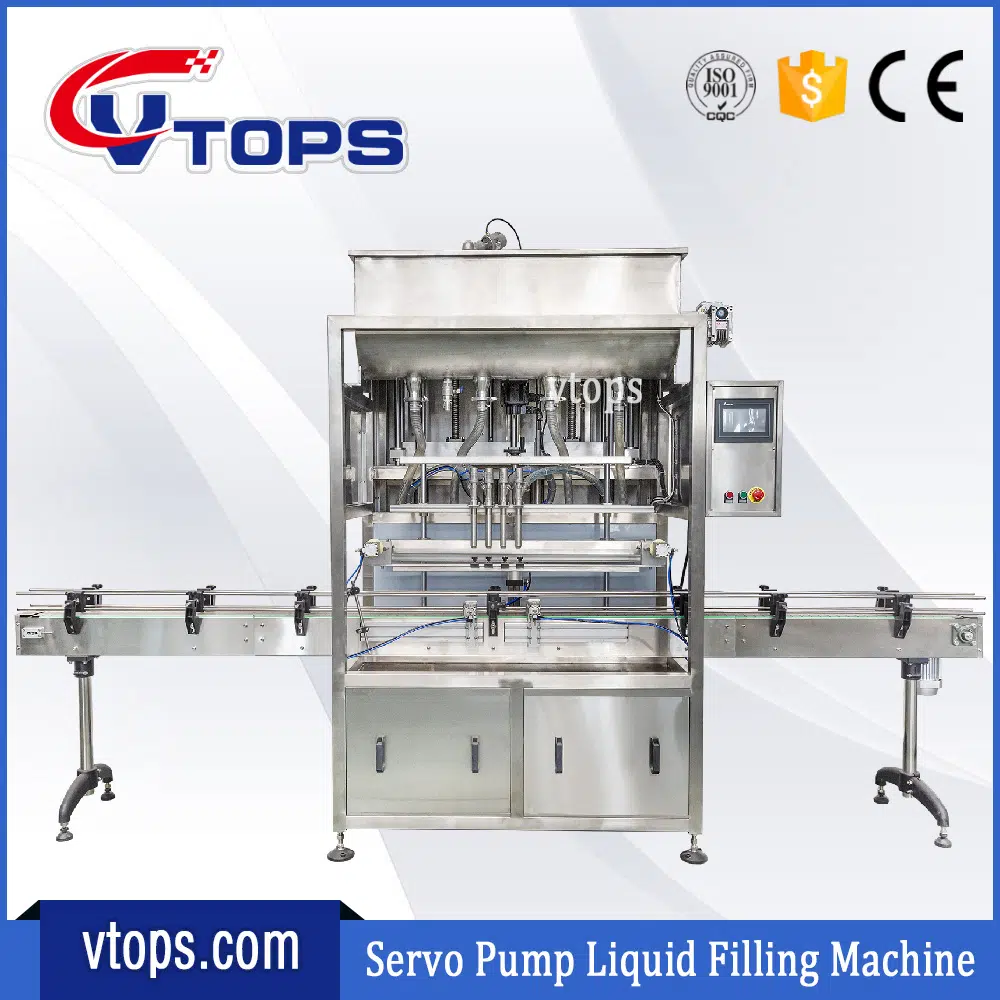
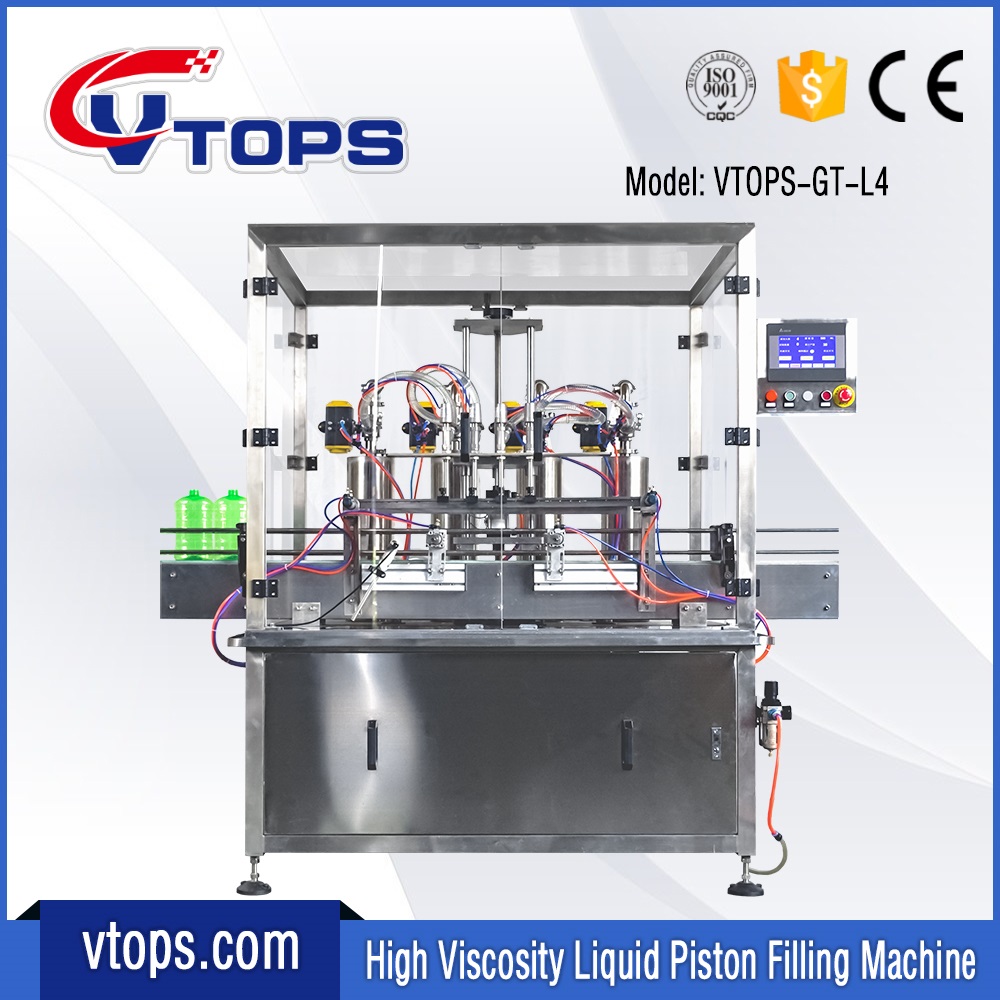
Powder Bottle Filling Machines
A Powder Bottle Filling Machine is a designed to automate the process of filling bottles or containers with powdered products. These machines are commonly used in industries such as spices seasoning, powdered milk, talcum powders, powdered pesticides, building powders, and powdered supplements, where powdered substances need to be accurately and efficiently packaged.
There are different types and configurations of powder bottle filling machines available, depending on factors such as the nature of the powder (fine, coarse, free-flowing, etc.), required filling accuracy, production volume, and automation level. These machines can vary in terms of filling mechanism, capacity, and additional features to suit specific industry needs.
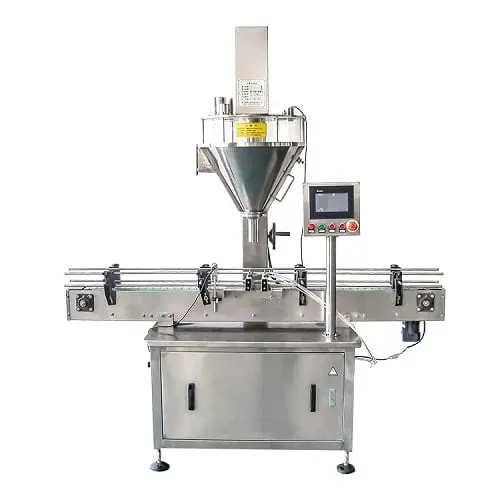
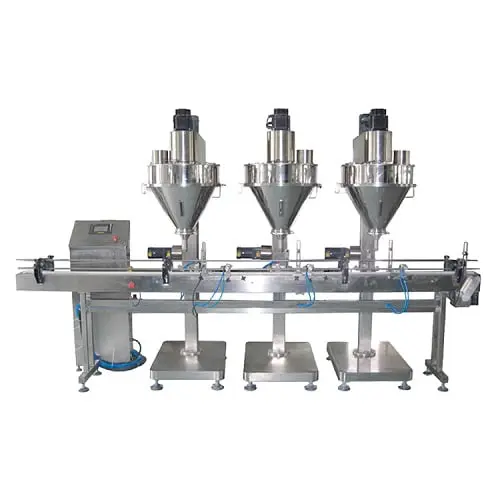
Granule Bottle Filling Machines
A Granule Bottle Filling Machine is designed to automate the process of filling bottles or containers with granular or small particle products. These machines are commonly used in industries such as granulated sugar, salt, rice, beans, lentils, nuts, granular fertilizers, granular herbicides, granular polymers, sand, pet food, and cereal, where granular substances need to be accurately and efficiently packaged.
There are different types and configurations of granule bottle filling machines available, depending on factors such as the nature of the granules (size, shape, flow characteristics, etc.), required filling accuracy, production volume, and automation level. These machines can vary in terms of filling mechanism, capacity, and additional features to suit specific industry needs.
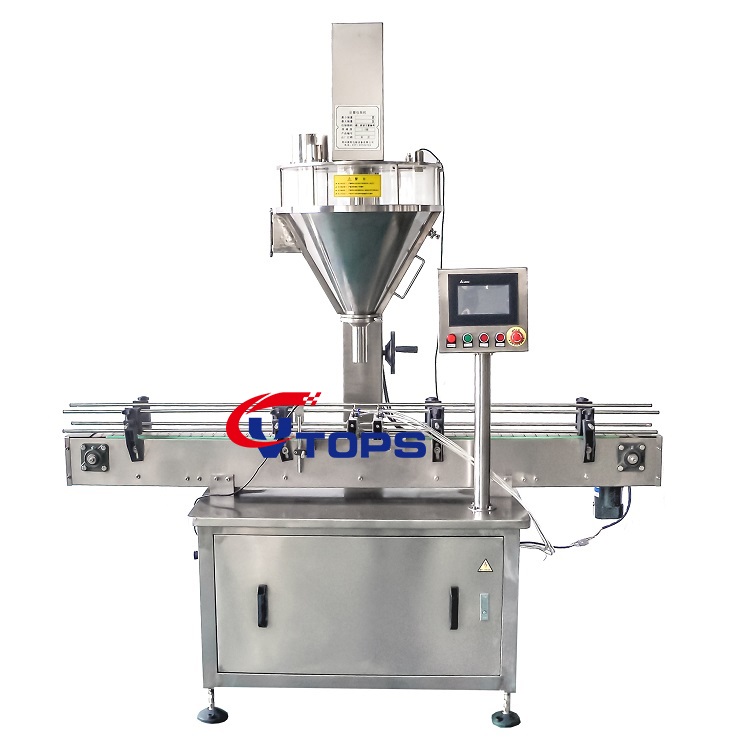
Paste Bottle Filling Machines
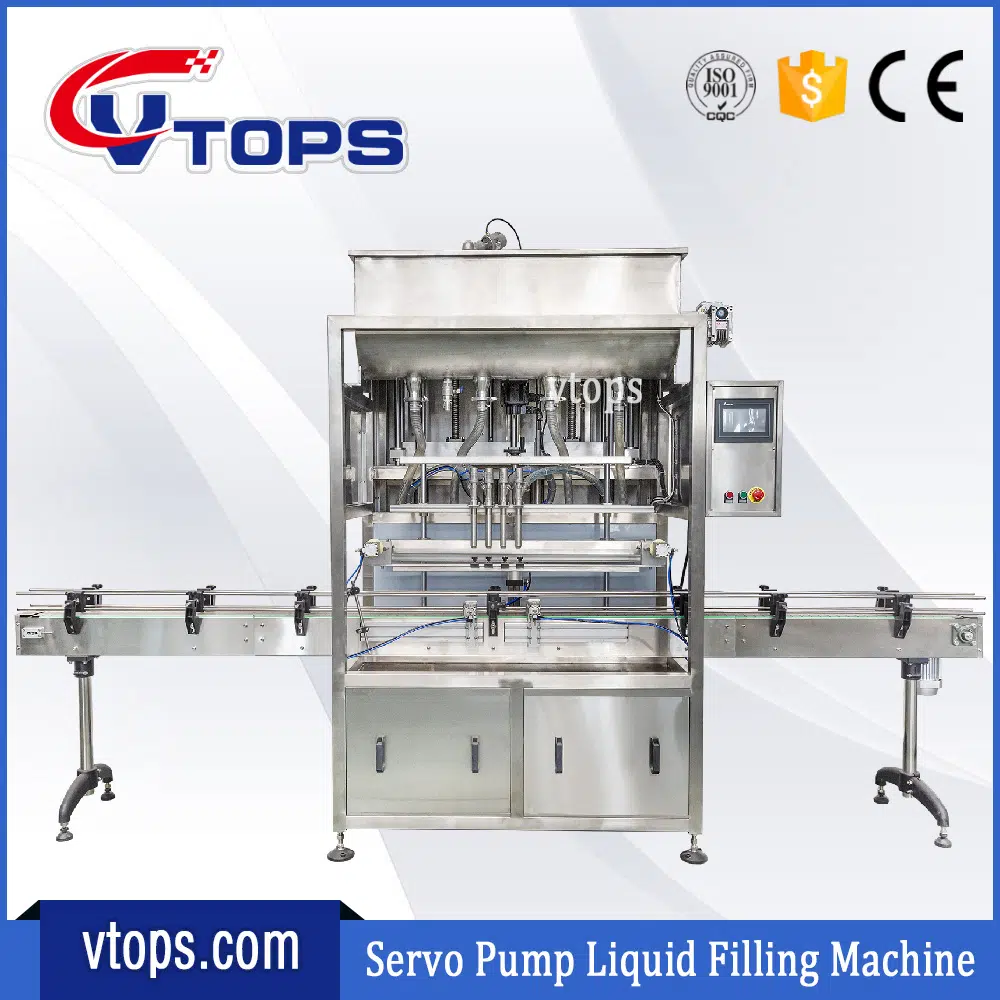
Aerosol Bottle Filling Machines
An Aerosol Bottle Filling Machine is specifically designed to automate the process of filling aerosol cans or bottles with various products, typically in the form of liquids, gases, or suspensions. These machines are commonly used in industries such as deodorants, sprays, perfumes, fresheners, insecticides, disinfectants, lubricants, rust inhibitors, inhalers, and nasal sprays, where aerosol products need to be accurately and efficiently packaged.
There are different types and configurations of aerosol bottle filling machines available, depending on factors such as the type of product being filled, required filling accuracy, production volume, and automation level. These machines can vary in terms of filling mechanisms, propellant handling systems, capacity, and additional features such as capping sytems to suit specific industry needs.
Gas Bottle Filling Machines
A Gas Bottle Filling Machine is designed to automate the process of filling gas cylinders or bottles with various gases, such as liquefied petroleum gas (LPG), compressed natural gas (CNG), oxygen, nitrogen, helium, and more. These machines are commonly used in industries such as gas distribution, welding and cutting, healthcare, laboratories, and industrial applications where gases need to be accurately and efficiently packaged.
There are different types and configurations of gas bottle filling machines available, depending on factors such as the type of gas, cylinder size, required filling accuracy, production volume, and automation level. These machines can vary in terms of filling mechanisms, pressure control systems, capacity, and additional safety features to meet specific industry requirements and standards.