Metal Foreign Objects Found In Frozen Food? Frozen Food Metal Detector Work Really Well!
According to a report by NHK TV in Japan on July 5, 2022. A Japanese Foods Refrigeration Company said it produced frozen Takoyaki mixed with metal flakes. Then, the Foods Refrigeration Company announced an emergency recall of its products produced on the same production line. They expect to recycle more than 4 million packages of frozen food. At the same time, some consumers point out foreign objects were mixed in the goods in late June. After investigation, the foreign object is an aluminum metal sheet. They may have been scraped off part of the line equipment and mixed into the food. The Foods Refrigeration company stated it will recall 6 types of frozen food including “Frozen Takoyaki”, with a total of about 2.94 million packs. In addition, the company has issued an apology, saying it will strengthen management.
It is a consensus that food safety is no trivial matter. As soon as this incident came out, there were also many consumers and investors concerned. Relevant personnel asked whether there is equipment in the food machinery industry to meet the needs of metal foreign body detection and for food production enterprises to use. Today, I will bring consumers a brief understanding of the application of metal detectors in food production.
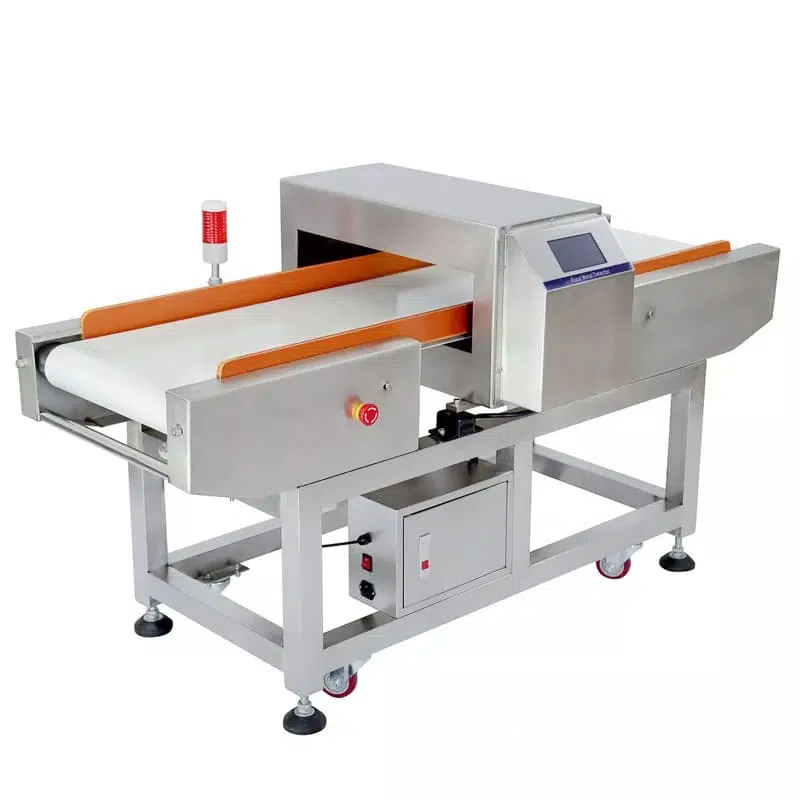
Although the production processes and production links of various types of food are different in food production. However, they are all inseparable from raw materials, labor, production environment and production equipment. These are also some of the factors that have an important impact on food quality and safety. Focusing on several reasons that may lead to the appearance of metal foreign bodies in food, consumers may be able to have a clearer understanding.
First, in large-scale food production, it is difficult to distinguish carefully if needles and metal wires are mixed with food raw materials such as meat and grains for processing. Second, although many food production lines are accelerating their automated production capacity. However, labor still plays a very important role in some key links in the food industry. Specifically, jewelry, hairpins, pins, buttons carried by workers may fall off in research from Gibson (2000). This can lead to food safety issues.
Furthermore, during the application and maintenance of a large number of food processing machinery, there may also be situations such as falling metal fragments and items being left behind. It may also contaminate the food. Based on NHK TV News, the Foods Refrigeration Company investigated the preliminary attribution of metal-containing foreign bodies in food. It is because part of the equipment in the production line such as a screw scraped off and mixed into the food.
In summary, it is necessary to carry out metal detection in food production and processing. At present, the methods used for foreign body detection in food mainly include:
- a. Manual detection
- b. Light inspection
- c. Touch Screen
- d. Magnetic separation
- e. Metal detection
- f. X-ray detection
However, considering the factors of detection effect, efficiency, and cost. Because of the many advantages of metal detectors that are cheap but easy to use, it is become the fastest growing and most commonly applied detection method in recent years.
Food Metal Detectors are mainly based on the principle of electromagnetic induction. And, through the induction of electromagnetic field and metal to achieve the effect of meat, dairy products, frozen food, pickled food, bakery, and other products. Then, it can detect magnetic and non-magnetic metals: such as iron, nickel, cobalt, copper, aluminum, and stainless steel. When food or other items pass through a metal detector with conveyor belt, it can complete a wide range of foreign body detection. Among such devices, the first is expanding with the application of information technology such as high-speed digital signal processing and intelligent algorithm technology (Martínek et al., 2015). These technologies will help to further improve the accuracy and stability of foreign object detection.
Meanwhile, many companies now have launched exclusive metal detectors for sub-categories for multiple types of food processing (Martínek et al., 2015). Including but not limited to frozen food metal detector. This includes tweaks and improvements to the functionality of the metal detector. Then, the improvement can better meet the inspection needs of different products and different production lines with flexible rejection methods. To achieve the purpose of improving the foreign body removal efficiency.
In conclusion, food safety is an unbreakable bottom-line issue. For the main body of food business, it is necessary to strengthen the standardized operation and inspection in the production process. And keeping the food safety line of defense is the key point of development. For the upstream food packaging machinery industry, it is also necessary to actively promote the optimization and upgrading of inspection and testing instruments. Finally, the company could provide high-quality services for the food industry with high-quality machines.