Multi-head weighers, also known as combination scales, stand as a pinnacle of efficiency, precision, and dependability in the realm of weighing machines. Developed and popularized by Ishida in the 1970s Wikipedia, these machines have seamlessly integrated into the global food industry. Since their inception, they have undergone redevelopment and production by numerous manufacturers worldwide, cementing their status as indispensable tools in modern packaging processes.
Nowadays, manufacturers globally are reimagining and reproducing these machines to meet the evolving needs of the industry. Some prominent manufacturers have specialized adaptations, tailoring multi-head weighers for specific purposes and functionalities. Examples include multi-head weighers for frozen foods, meats, caviar, noodles, and other applications.
This guide explores from a technical perspective how multi-head scales works, the purposes of use, and considers when choosing a multihead weigher. For those who are evaluating their first packaging automation project using multi-head weighers or starting from semi-automatic packaging weighing systems, you will benefit from the explanations provided in this article.
Parts of Multihead Weigher
A multi-head weigher is a complex weighing system consisting of multiple key components, each with its specific name and primary role. The following are the main components of a multi-head weigher and their functions:
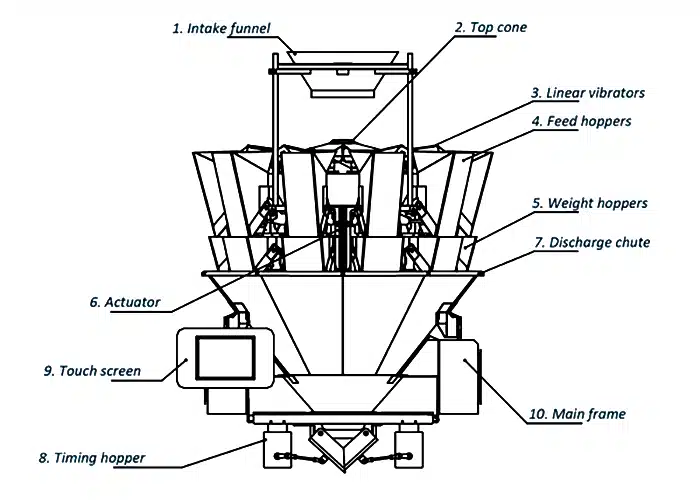
1. Intake Funnel:
Intake funnel is the entry point where the raw materials or products are fed into the multihead weigher from feeding machine. It helps in directing the flow of items towards the weighing system.
2. Top-cone:
Positioned above the linear vibrators, the top cone helps in distributing the product evenly across the linear vibrators and feed hoppers.
3. Linear vibrators:
Linear vibrators are vibratory conveyors that help in the controlled and uniform flow of the products towards the feed hoppers.
4. Feed hoppers:
Feed hoppers collect and hold the products before they are released (Feed) into the Weight Hoppers. Each linear vibrator corresponds to a set of feed hoppers.
5. Weight hoppers:
Weight hoppers are the key components responsible for product weighing and is responsible for weighing the weight of the products in the hopper. They come in different sizes (1.8 liters, 3 liters, and even larger) to accommodate various product weights.
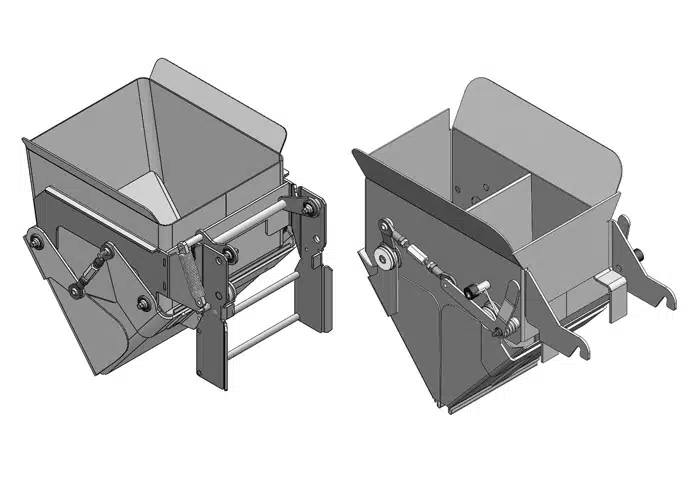
6. Actuator:
The actuator controls the opening and closing of the gates at the bottom of the weight hoppers, allowing the measured product to be discharged.
7. Discharge chute:
Located below the weight hoppers, the discharge chute directs the weighted product to the next stage of the packaging process.
8. Timing hopper:
Timing hopper is an intermediate hopper that temporarily holds the weighed product until it’s ready to be discharged, providing better synchronization with the packaging process.
9. Touch screen:
The user interface for controlling and monitoring the multihead weigher. Operators can set parameters, monitor the weighing process, and make adjustments using the touch screen.
10. Main frame:
The main structural framework that holds and supports all the components of the multihead weigher, providing stability and rigidity to the entire system.
These components work together to ensure accurate and efficient weighing and packaging of products in a production line.
How Does a Multihead Weigher Work?
How does a mulihead weigher work? | MULTIPOND
Here’s a step-by-step explanation of how a multihead weigher works:
Step 1: Material Infeed:
Bulk or loose products are typically fed into the multihead weigher through a feeding system. The feeding system can be a sloped conveyor or a bucket elevator that transports the materials to the top of the Multihead Weigher machine.
Step 2: Product Dispersion:
The product is then evenly distributed among a number of individual feed hoppers or buckets, from which it is released into the weight hopper. This is achieved through various methods, such as vibrating pans, rotating cones, or other dispersion mechanisms.
Step 3: Weighing Process:
Each weight hopper is equipped with a load cell or a weighing sensor that continuously measures the weight of the product inside it. As the product is dispensed into the weigh hoppers, the system continuously updates the weight readings.
Step 4: Combination Calculation:
The multihead weigher’s computerized control system calculates various combinations of the individual weigh hopper weights to achieve the target total weight. The goal is to find a combination that meets the specified weight requirement with the highest accuracy.
Step 5: Product Release:
Once the optimal combination is determined, the machine opens the gates or valves of the selected weigh hoppers simultaneously, allowing the products to fall into the packaging machine or downstream conveyors.
Step 6: Replenishment and Continuous Operation:
After a weighing operation (once the products are released from the weight hoppers), the empty weigh hoppers are replenished with the additional batch product, and the process repeats in a continuous cycle. This ensures a constant and efficient flow of weighed products.
Feedback and Adjustments:
The VTOPS multihead weigher’s software continuously monitors and adjusts parameters to optimize accuracy. Feedback mechanisms help in fine-tuning the system based on real-time data, increasing the overall efficiency of the packaging process.
Why Use a Multihead Weigher?
Multihead weighing systems offer several advantages, such as speed, accuracy, customization, and integration capabilities, that can contribute to operational efficiency, cost savings, and product quality, particularly in packaging, food processing, and manufacturing industries. Here are some ways in which multi-head weighing can help a business:
Ⅰ, Speed and Accuracy
Multihead weighers are equipped with weighing sensors that allow for the rapid and precise handling of bulk products while still adhering to specific weight targets. This ensures that each product package contains the specified weight, reducing the chances of overfilling or underfilling. The continuous refilling of weigh buckets enables higher speeds compared to manual weighing, contributing to process automation.
Ⅱ, Flexibility in for Different Products
Multihead weighers are versatile and can be customized for various product types. This adaptability makes them suitable for a wide range of industries, addressing diverse production challenges. Whether dealing with snacks, fresh produce, frozen food, meat, seafood, hardware accessories, vegetable salads, pickles, noodles, shredded tobacco or other items, a multihead weigher can be tailored to meet specific requirements. It is valuable for businesses dealing with a diverse range of products.
Ⅲ, Consistent Product Quality
Accurate weighing helps minimize giveaway (overfilling) and waste, and maintaining consistent product weights. The products consistent enhance the overall quality and presentation of the final packaged goods. This is crucial for maintaining customer satisfaction and meeting regulatory standards.
Ⅳ, Automation and Increased Efficiency
Automated weighing systems of multi-head weighers can handle tasks that would not require human intervention. This not only speeds up the entire process but also frees up human resources for more value-added tasks. Moreover, automated weighing processes contribute to minimizing the risk of human error. The multihead weigher machines are programmed to follow precise instructions consistently, eliminating the variability that may arise from manual intervention. The automatic weighing system improves the accuracy and increases the efficiency of the packaging process.
Ⅴ, Quick Changeovers:
Multihead weighers are designed for quick and efficient changeovers between different products or packaging sizes. This feature is valuable for businesses with diverse product lines.
Ⅵ, Integration with Other Packaging Equipment:
Multihead weighers can be seamlessly integrated with other packaging equipment, such as bagging machines, tray fillers, or vertical form-fill-seal (VFFS) machines, creating a cohesive and automated packaging line. Even integrated into more extensive production lines alongside other equipment such as checkweighers and product inspection systems.
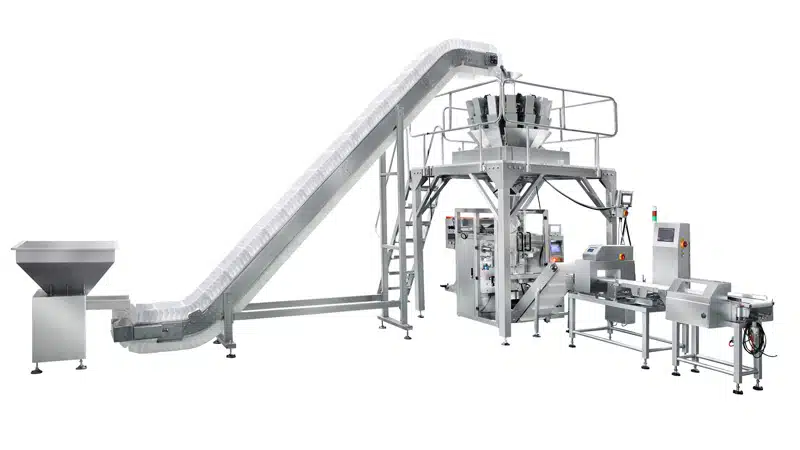
Conveyor systems facilitate the smooth movement of products from one area to another, minimizing the need for manual handling and intervention. This integration enhances overall production line quality and accuracy, consistently delivering outputs that meet specifications and customer expectations.
Ⅶ, Enhanced Traceability:
Some multihead weighing systems made by VTOPS come with software that provides data tracking and traceability, which can be essential for quality control, compliance, and process improvement. Monitoring and analyzing data allows for process optimization, increased efficiency, and error reduction. Additionally, the system enables data export to USB drives, facilitating comprehensive record-keeping and ensuring easy storage of crucial information for future reference. This combination of features contributes to a streamlined production process with enhanced reliability and traceability.
Applications of Multihead Weighers
Common applications of multihead weighers include:
1. Food Industry:
- Snack Foods: Multihead weighers are widely used for packaging snacks like chips, nuts, and candies.
- Fresh Produce: They are employed for weighing and packaging fruits, vegetables, and salad items.
- Frozen Foods: In the frozen food industry, multihead weighers help with the accurate weighing of items like frozen fruits, vegetables, and ready-to-eat meals.
2. Confectionery:
• Multihead weighers are used for weighing and packaging various types of confectionery, including chocolates, candies, and gummies.
3. Pet Food Industry:
• In the pet food industry, multihead weighers help with the precise weighing and packaging of dry pet food.
4. Bakery Products:
• Multihead weighers are employed for packaging bakery products such as bread, pastries, and cookies.
5. Non-Food Items:
• They are used for weighing and packaging non-food items like hardware, fasteners, and small components.
6. Pharmaceuticals:
• In the pharmaceutical industry, multihead weighers assist in accurately weighing and packaging tablets, capsules, and other medications.
7. Chemicals and Powders:
• Multihead weighers are used in industries dealing with chemicals and powders, ensuring accurate measurements for products like detergents, fertilizers, and powdery substances.
8. Hardware and Fasteners:
• Multihead weighers can be employed for the accurate counting and packaging of small hardware items, nuts, bolts, and screws.
9. Fresh Meat and Seafood:
• In the meat and seafood industry, multihead weighers contribute to the precise weighing and packaging of fresh meat, poultry, and seafood products.
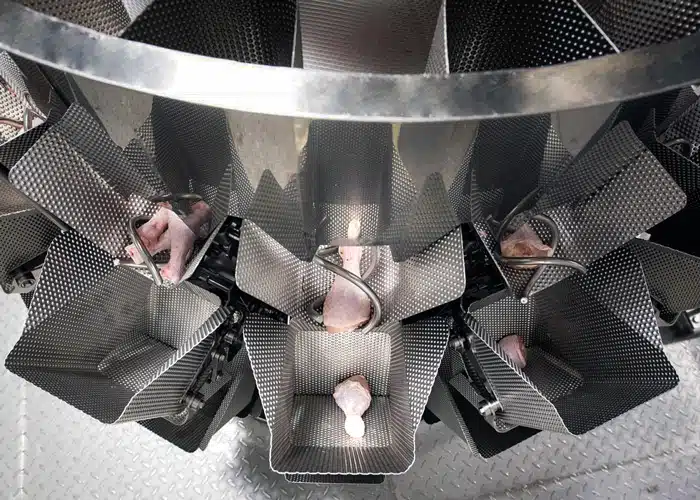
10. Dairy Products:
• Multihead weighers are used for packaging dairy products such as cheese, butter, and yogurt.
11. Ready Meals:
• They are employed in the packaging of ready-to-eat meals, ensuring accurate portioning and packaging.
12. Coffee and Tea Industry:
• In the coffee and tea industry, multihead weighers assist in accurately measuring and packaging coffee beans, ground coffee, tea leaves, and other related products.
13. Automotive Components:
• Multihead weighers can be used for counting and packaging small automotive components, ensuring precision in the assembly process.
14. Cosmetics:
• In the cosmetic industry, multihead weighers help with accurate weighing and packaging of products such as powders, creams, and cosmetic samples.
These applications showcase the versatility of multihead weighers across different industries where efficient and precise weighing is crucial for the production and packaging processes.
What to Consider When Choosing a Multihead Weigher?
Here’s a summary of the key considerations when choosing a Multihead Weigher:
Number of Heads:
The number of weigh heads influences the speed and accuracy of the system. More heads generally lead to faster and more accurate weighing. Consider the volume of bulk products you need to process and choose a machine with an appropriate number of heads. VTOPS offers multihead weighers ranging from 10 to 36 heads to suit your needs.
Material Mixing:
If you need to mix different products in the same container, look for a multihead weigher with material mixing capabilities. Some machines allow partitioned weighing, enabling you to weigh multiple products simultaneously in designated areas.
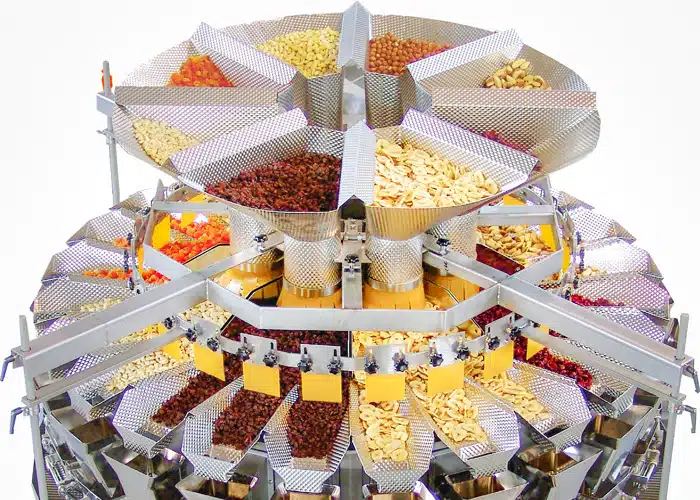
Surface Types:
Consider the surface types of the weigh buckets based on the characteristics of your products. Textured or contoured surfaces may be necessary for sticky products, while smooth surfaces are suitable for dry materials.
Vibration:
Adjust the vibration settings based on the material being processed. Stickier products may require more vibration for efficient movement, while delicate products may need minimal vibration to prevent damage.
Bucket Size and Shape:
Choose the appropriate bucket size and shape based on the size and characteristics of your products. Consider factors such as ease of cleaning, especially for sticky substances, and whether a standard or custom shape is more suitable.
IP Rating:
The IP rating indicates the level of protection against dust and water ingress. Select an IP rating that suits your production environment, considering factors like product stickiness, cleaning frequency, and compliance with hygiene standards.
Maximum Weighing Range:
Consider the maximum weight the multihead weigher can handle. This is crucial for processing larger products or achieving higher throughput. Evaluate the weighing range, the weight of each load cell, and the available discharge range for optimal performance.
Speed:
Evaluate the processing speed of the multihead weigher in terms of weighed portions per minute. Balance speed with accuracy, especially when handling fragile or delicate products.
Footprint:
Consider the space available in your production area. Choose a multihead weigher with a footprint that fits your space constraints while still delivering the required performance.
Additional Extras:
Explore optional features that can enhance the functionality of the multihead weigher, such as waste reduction mechanisms, touchscreens, data collection capabilities, and automatic feed controls. Ensure these extras align with your production goals.
Integration with Packaging Line:
Confirm that the chosen multihead weigher can seamlessly integrate with your packaging line, including compatibility with other equipment like bagmakers and inspection systems.
Price:
While considering the budget, weigh the cost against the benefits and long-term return on investment. A more efficient and reliable multihead weigher may justify a higher upfront cost through increased productivity and reduced operational issues.
By carefully evaluating these factors, you can choose a multihead weigher that aligns with your production needs and contributes to a streamlined and efficient packaging process.
Where to Find the Right Multi-head Weigher
VTOPS provides comprehensive support, including employee training, mechanical debugging, and customization services tailored to your needs. Moreover, all products offer a two-year free warranty, ensuring your machine’s longevity and optimal performance. We also encourage you to explore long-term service contracts and spare parts management solutions for added peace of mind. Contact Vtops today to discuss your multi-head weighing requirements and unlock a world of precision, reliability, and exceptional customer support for your business. Additionally, the Vtops local service agent program is open for applications, welcoming distributors with a commitment to outstanding service to contact us.