How Automated Palletizing Solutions Improve Efficiency, Reduce Costs, and Enhance Workplace Safety in Modern Industrial Production
As labor costs continue to rise and production volumes increase, replacing heavy and repetitive manual labor with machinery has become an inevitable trend. Particularly in high-risk industries like chemicals, harsh working environments can impact workers’ health. The introduction of palletizing robots significantly enhances production safety.
1. Economic Benefits of Palletizing Robots
From an economic perspective, a fully automated palletizing machine can replace six workers, operating 24/7 to greatly reduce labor costs and workload.
Comparison Item | Manual Palletizing | Automated Palletizing |
---|---|---|
Efficiency | 100 bags/hour | 800 bags/hour |
Labor Cost | High | Low |
Operational Cost | High | Low (5KW Power) |
Stability | Affected by workers’ condition | Highly stable |
2. What is a Palletizing Robot?
A palletizing robot is an automated system equipped with a robotic arm designed to pick, sort, and stack items onto a pallet in an organized and efficient manner. These robots are typically positioned at the end of a production line and play a crucial role in optimizing warehouse and logistics operations.
The concept of mechanized palletizing dates back to 1948 when the first mechanized palletizer was designed, built, and installed by a company formerly known as Lamson Corp [1]: Palletizer on Wikipedia. Since then, palletizing technology has evolved significantly, with modern palletizing robots now widely used across industries such as packaging, logistics, manufacturing, and warehousing. These advanced systems help streamline processes, improve efficiency, and reduce labor costs. Their ability to consistently stack and arrange goods with precision makes them an essential tool in modern automated facilities.
Milk Powder Cans Boxing Robot Palletizing Production Line, Tin Cans Packaging in Paper Carton Box
3. Understanding the Types of Palletizing Robots
Palletizing machines come in various types based on their structure and function:
1). Robotic Palletizer (Robotic Arm Palletizer)
- Utilizes a robotic arm for fast and efficient palletizing.
- Can handle up to 800 bags per hour.
- Ideal for medium and large-scale enterprises with high automation requirements.
2). High-Level Palletizer
- One of the most common types, offering efficiency of approximately 450 bags per hour.
- Simple programming, stable structure, and easy operation.
- Suitable for production lines with higher throughput.
3). Cartesian Palletizer
- Uses a four-axis motion system, requiring minimal floor space and offering flexible installation.
- Best for scenarios where load capacity requirements are lower.
4). Column Palletizer
- Combines features of robotic and Cartesian palletizers.
- Capable of servicing 2–3 production lines simultaneously, increasing operational flexibility.
4. Key Advantages of Palletizing Robots
- Increased Efficiency: Works continuously without fatigue, improving productivity.
- Consistency & Accuracy: Ensures uniform stacking and placement of products.
- Space-Saving: Compact designs optimize floor space in warehouses.
- Safety & Ergonomics: Reduces workplace injuries related to manual lifting and stacking.
- Flexibility: Can be programmed for various palletizing patterns and product types.
5. How to Choose the Right Palletizing Robot?
Selecting the right palletizing robot requires considering product type, speed requirements, space limitations, and budget. Here are the key factors to focus on:
1). Define Your Requirements
- Identify product type (boxes, bags, drums, etc.), weight capacity, and palletizing speed (cases per minute).
- Determine pallet size and stacking patterns for efficient space utilization.
2). Choose the Right Robot Type
- Articulated Robots (4-Axis/6-Axis): High flexibility, ideal for complex palletizing.
- Gantry (Cartesian) Robots: Best for heavy loads and precise stacking.
- SCARA Robots: Fast but limited in reach and weight capacity, suitable for small, lightweight items.
- Collaborative Robots (Cobots): Safe for human interaction, best for low-speed, flexible applications.
3). Key Performance Factors
- Payload Capacity: Ensure the robot can handle the heaviest product.
- Reach & Work Envelope: Must cover the palletizing area efficiently.
- Speed & Cycle Time: Matches production requirements.
- End-of-Arm Tooling (EOAT): Choose from vacuum suction, clamps, or fork grippers based on product type.
- Software & Integration: Ensure compatibility with existing automation systems.
4). Layout & Space Planning
- Assess available floor space and ensure smooth conveyor integration for loading and unloading.
5). Cost & ROI Evaluation
- Consider the initial investment, operating costs, and labor savings to calculate the return on investment (ROI).
6). Safety & Compliance
- Ensure the robot meets ISO, OSHA, and industry safety standards.
- Traditional palletizers require protective fencing, while cobots should have built-in safety features.
7). Future Scalability
- Ensure the system can scale up for higher production and adapt to new packaging formats.
6. Real-World Applications of Palletizing Robots
Case 1: Food Industry – Doubling Production Efficiency
A well-known food processing company integrated a VTOPS robotic palletizer, reducing labor costs by 30% and increasing production efficiency by 40%. With smart grouping capabilities, the system adapts to product characteristics, reducing product damage and optimizing storage management.
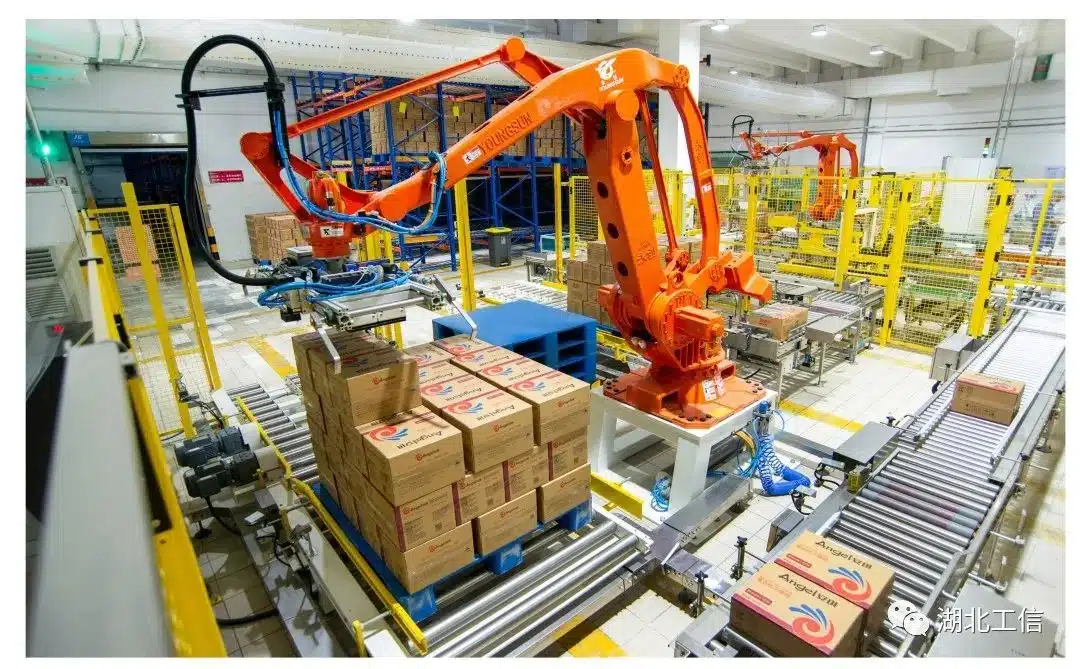
Case 2: Chemical Industry – Enhancing Workplace Safety
A major chemical manufacturer faced high risks due to dusty environments and manual handling. By deploying a fully automated palletizing system, worker exposure to hazardous materials decreased significantly, ensuring compliance with strict safety regulations while improving production efficiency.
Case 3: Beverage Industry – Smart Supply Chain Optimization
A global beverage company faced challenges in high-speed bottle handling. By implementing a high-speed VTOPS robotic palletizer, they increased palletizing capacity to 1,200 cases per hour—three times more efficient than manual operations—streamlining their supply chain.
Conclusion
Palletizing robots play an increasingly crucial role in modern manufacturing, understanding and applying them can significantly improving efficiency, reducing labor costs, and enhancing workplace safety. As automation technology advances, these intelligent machines will further revolutionize industrial production, leading to smarter, more efficient operations.
References
[1] Palletizer on Wikipedia: The first mechanized palletizer was designed, built, and installed in 1948 by a company formerly known as Lamson Corp.