Some Problems You Will Meet When Picking an Auger Filler
Basic Structure
The primary dry powder filling machine comprises an auger filler and an optional screw conveyor feeder. The outlet of the screw conveyor feeder is connected to the top of the hopper of the auger filler by a soft connection. The dry powders in the hopper of the screw conveyor feeder will be conveyed to the hopper of the auger filler by screw feeder blades.
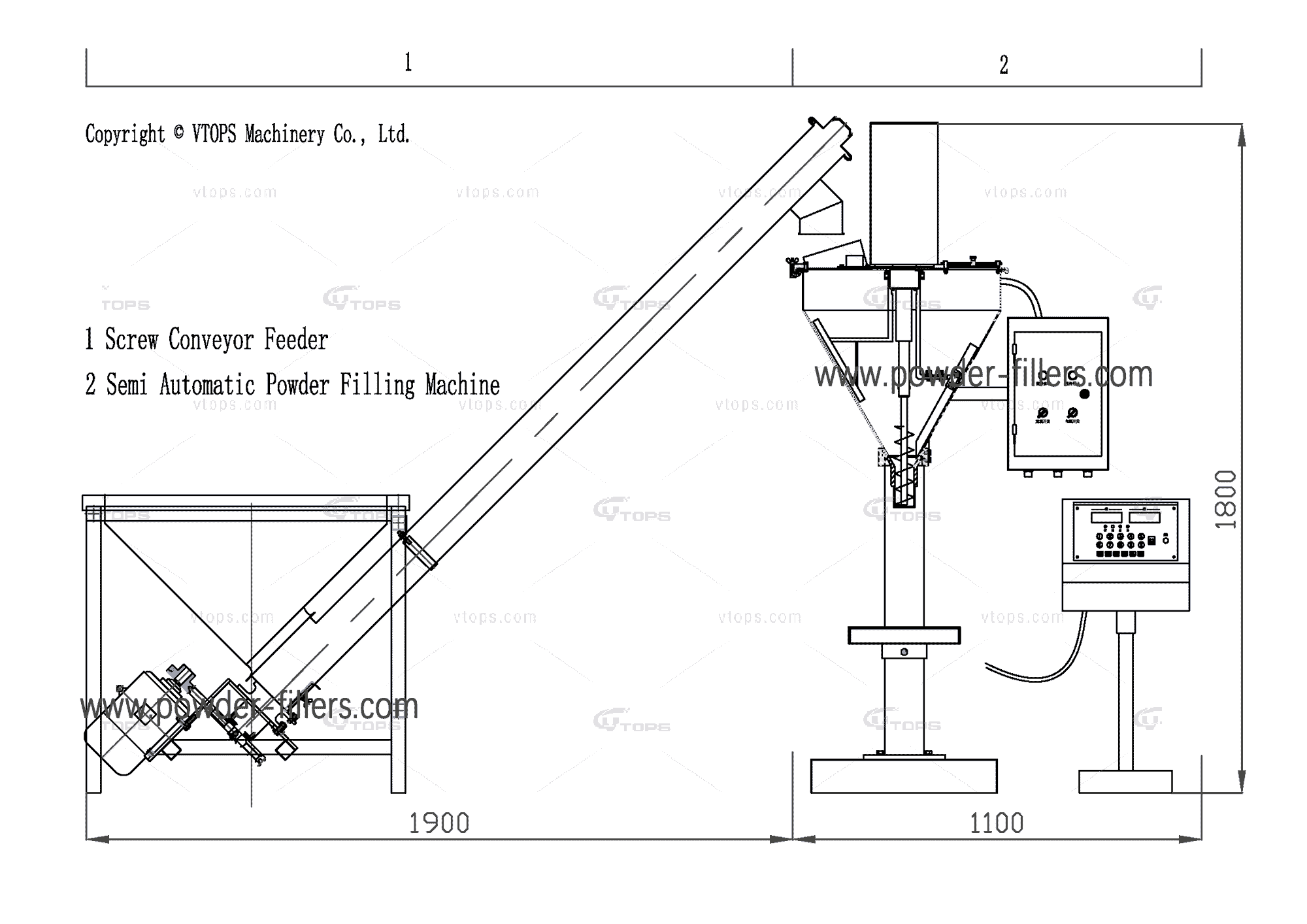
Dry Powder Filling Machine
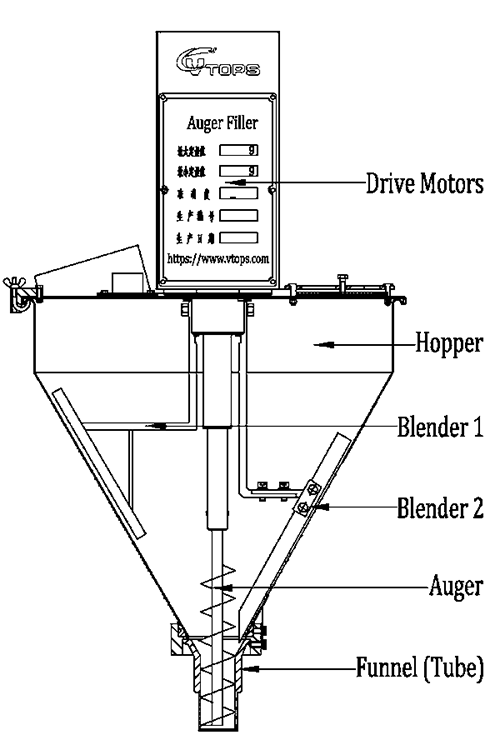
Basic Structure of Auger Filler
Double blender blades mounted inside the hopper of auger filler and arranged at 180 degrees. The blender-blades are in constant rotation when loading and filling. To ensure dry powders uniformed distribution in the hopper of auger filler which powders delivered from the hopper of screw conveyor feeder. And the dry powders uniformly enter the auger under the influences of gravity and blades, thereby ensuring the filling precision and continuity of the dry powders.
Closed Design
Dust Removal Equipment
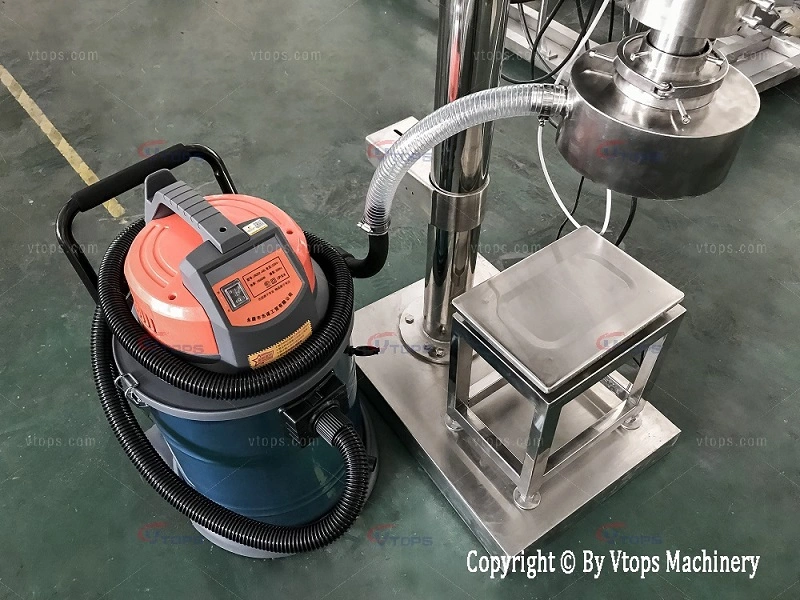
Dust Removal Device (Dust Cover)
A dust removal device can be added if necessary.
Ways of Filling
Fill By Volume
FILL-BY-VOLUME is also called VOLUME-BASED FILLING or OFF-LINE SCALE WEIGHING FILLING. For everyday applications, every food packaging has a net content weight. The constant filled weight is the result of our often-called quantitative filling.
Fill By Weight
FILL-BY-WEIGHT is also called WEIGHT-BASED FILLING or IN-LINE SCALE WEIGHING FILLING. For customers with high precision requirements, they often care about error as low as 0.1%. So, the high precision research and development has always been the unremitting pursuit of professional auger powder filling machine manufacturers.
Vtops Machinery newly designed and developed a high-precision double-head auger filler which has the function of online weighing system, and the filling error is within 1 gram for 1kg. At present, the high-precision double-head auger filler has been exported to German and Australian milk powder manufacturers and received excellent feedback.
Fill By Vibrating
Different hoppers have different functions. So far, VTOPS company have three types of hoppers: Primary Hopper, Monitorable Hopper, and Split Hopper.
The primary hopper is a powder storage container made of a complete stainless steel coil. This hopper has been eliminated by us.
Advantage: Lower cost.
Disadvantage: Can’t see the state inside the hopper, poor quality.
The monitorable hopper is made of transparent plexiglass and 304 food-grade stainless steel to form the inverted cone hopper. All auger filler machines of VTOPS are currently equipped with the monitorable hopper or an upgraded version of this hopper.
Advantage: The clear plexiglass allows the operator to easily and clearly see the level of powder in the hopper, and more importantly, it is easy to replace the screw.
Disadvantage: Can’t see the state inside the hopper, poor quality.
Having an easy-to-clean hopper in an auger filler machine offers several advantages, such as high flexibility that can meet the requirements of flexible production, especially in industries where hygiene and product purity are critical. Here are some key benefits of having a hopper that is designed for easy cleaning:
- Reduced Risk of Contamination: Easy-to-clean hoppers are less likely to harbor product residues, which can lead to cross-contamination between different products. This is particularly important in industries such as food, pharmaceuticals, and cosmetics, where product purity is essential.
- Faster Changeovers: Quick and efficient cleaning of the hopper simplifies product changeovers. When switching from one weight to another weight, it only takes 2 minutes to replace the different diameter metering auger parts if necessary. It will not affect the normal operation of the entire production line of the factory.
In addition, when switching from one product to another, operators can clean the hopper more rapidly, minimizing downtime and improving production efficiency. - Maintains Product Integrity: Some products can be sensitive to moisture, temperature, or foreign particles. An easy-to-clean hopper ensures that the previous product is thoroughly removed, reducing the risk of product contamination or degradation.
- Compliance with Regulations: Many industries have strict regulations and standards regarding equipment cleanliness and hygiene. An easy-to-clean hopper can help companies meet these regulatory requirements more easily.
- Extended Equipment Life: Regular and thorough cleaning of equipment components, including the hopper, can help extend the lifespan of the auger filler machine. Removing product residues and preventing buildup can reduce wear and tear on machine parts.
- Improved Product Quality: When a hopper is cleaned thoroughly between batches, product quality is maintained at a higher level. This is especially important for industries that rely on consistent product quality and uniformity.
- Reduced Product Waste: Easy cleaning reduces the amount of product left in the hopper after each batch. This means less product waste and cost savings over time.
- Enhanced Operator Safety: Cleaning equipment can sometimes involve exposure to cleaning agents or potentially hazardous materials. An easy-to-clean hopper can make the cleaning process safer for operators by minimizing their contact with the product.
- Quick Inspections: Easy access to the hopper simplifies visual inspections, allowing operators to check for any signs of wear, damage, or contamination more easily.
- User-Friendly Maintenance: Maintenance tasks, such as lubrication and inspection of mechanical components inside the hopper, become more straightforward with an easy-to-clean design.
In summary, an easy-to-clean hopper in an auger filler machine contributes to better product quality, compliance with industry regulations, reduced downtime, and improved equipment longevity. This makes it a valuable feature in industries where cleanliness and hygiene are of utmost importance.
Filling Motor
Servo Motor
High Precision and Accuracy: Servo motors provide precise control over the auger’s rotation, allowing for extremely accurate filling. This precision is crucial in industries where even minor variations in product quantity can lead to quality issues or regulatory non-compliance.
Consistency: Servo motors maintain a consistent speed and torque, ensuring uniform product dosing throughout the filling process. This consistency leads to reliable and repeatable results.
Machine self-protection: Servo motors equipped with overvoltage protection, overcurrent protection, and undervoltage protection have enhanced safety and reliability features to safeguard the motor and the connected equipment. These protection mechanisms help prevent damage to the servo motor and ensure its proper operation.
Stepper Motor
Stepper motors also have their advantages when used in auger filler machines. While they differ from servo motors in terms of operation and characteristics, stepper motors offer specific benefits that can be advantageous for certain applications. Here are the advantages of using stepper motors in auger fillers:
Cost-Effectiveness: Stepper motors tend to be more cost-effective than servo motors, making them an attractive choice for businesses with budget constraints. This cost savings can be significant, especially in smaller or less complex packaging operations.
Simplicity: Stepper motors have a straightforward design with fewer components and do not require feedback devices like encoders, which are common in servo systems. This simplicity can lead to easier installation and maintenance.
It’s important to note that stepper motors may not be as suitable for high-speed and high-precision applications as servo motors. The choice between stepper and servo motors depends on specific application requirements, budget considerations, and the desired level of control and precision. Stepper motors are often favored in simpler, cost-conscious auger filling setups, while servo motors excel in more complex and demanding applications where speed, accuracy, and flexibility are critical.
Convert of Metering Weight
In addition, the range of filling weight is also worth considering. Because the diameter of the funnel determines the speed and accuracy of the filling.
For example:
We are familiar with the water faucets and their diameters have a difference.
A water faucets with thick diameter have a fast flow rate, but have poor accuracy.
A water faucets with thin diameter have a slower flow rate, but have higher accuracy.
So, Vtops Machinery recommended diameter of the funnel (Diameter of Auger Fillers) is following:
Fill Weight | Recommended Diameter of Funnel |
---|---|
1g-5g | Customize |
5g-10g | φ20mm – φ25mm |
10g-50g | φ25mm – φ30mm |
50g-100g | φ30mm – φ35mm |
100g-500g | φ35mm – φ45mm |
500g-1000g | φ45mm – φ55mm |
1000g-5000g | φ55mm – φ65mm |
Tips:
- 1, All funnels are replaceable with each other. If you have any questions, please do not hesitate to Contact us.
- 2, The above table was updated in November 2021.